Serving highly regulated
medical markets
We combine deep AM process and material expertise to manufacture
high-end products for quality-critical medical applications.
Amnovis offers a high-quality and fast-turnaround process for 3D printing medical devices, covering patient-specific implants and volume production of standard components. We push medical device innovation by focusing on developing new medical device applications and validating state-of-the-art AM technologies, materials and related processes.
The Amnovis’ founders have a proven track record in metal AM that goes back until 2008. They were among the first to employ L-PFB for printing titanium medical devices, such as orthopedic and spinal implants. We enable customers to aim high and move fast, while removing hurdles in medical device development, validation and manufacturing. Our comprehensive AM workflow and production platform is entirely ISO 13485:2016 certified.
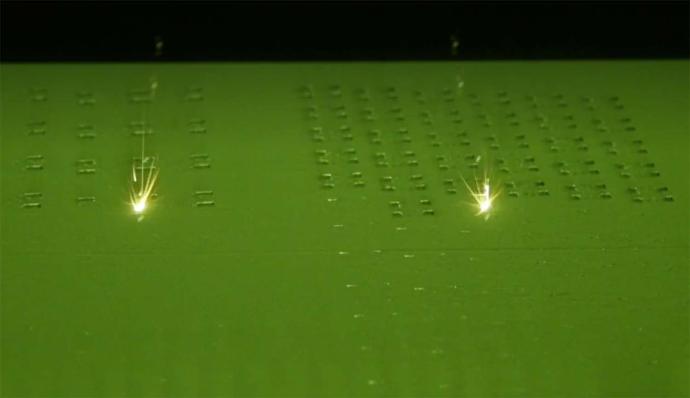
AM volume contract manufacturing
For Amnovis, innovation benefits from material and process enhancements as well as the ability to increase AM productivity. By scaling our manufacturing capabilities for quality-critical medical devices, we ensure faster delivery at lower cost, while maintaining our quality standards.
Our joint offering with selected partners covers the complete process. Overall, we maximize reliability, productivity, uptime and yield in our efforts to better serve titanium spinal cage and other medical device OEMs.
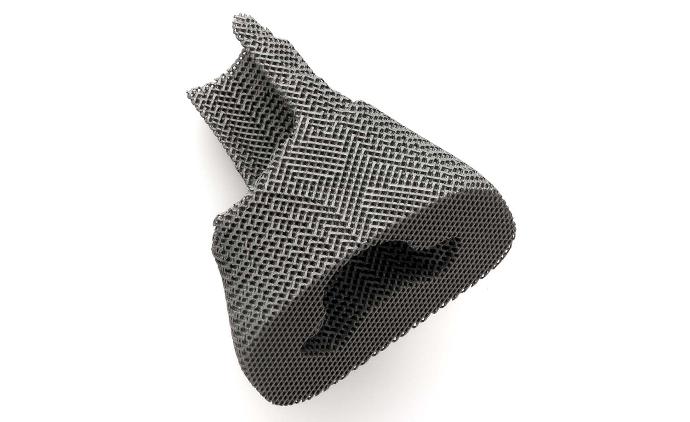
Patient-specific AM medical devices.
Today, we print patient-specific orthopedic and other custom devices using our comprehensive AM workflow and production platform. Years ago, the Amnovis’ founders were pioneers in employing L-PFB for printing the world's first patient-specific titanium lower jaw.
Next to metal AM, we also manufacture medical devices using stereolithography 3D printing. One example concerns patient-specific surgical guides designed to assist surgeons in precisely locating and accurately excising breast tumors.